Took a break from cleaning today and spent some time contemplating leveling feet. There are 8 Leveling feet and 8 “lagging” holes on the Monarch CK from what I can gather from the manuals and as witnessed on my machine. Basically 8 Holes are threaded for the leveling screws and the other 8 are unthreaded for lagging to the floor as suggested in the manual.
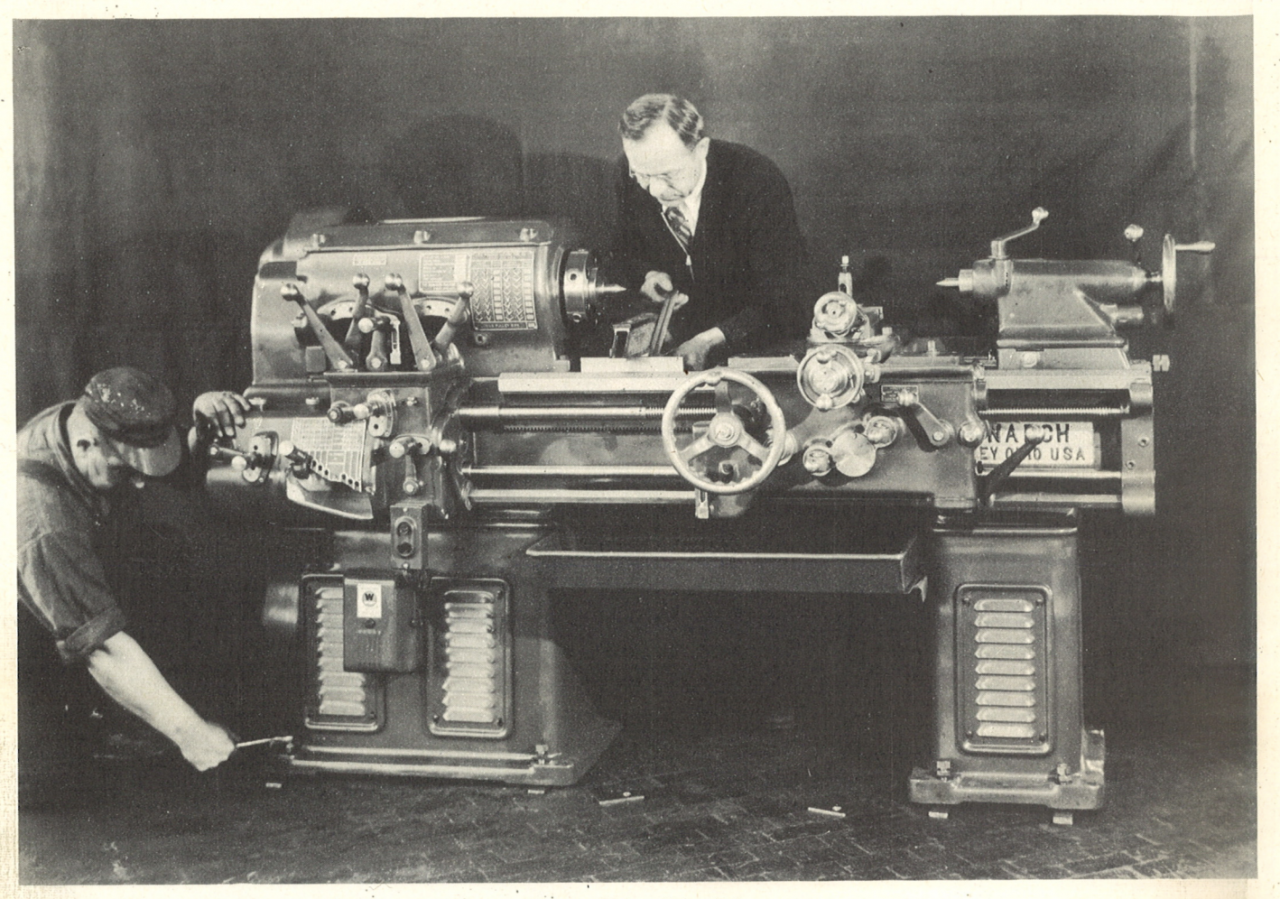
After closer inspection of my lathe two of the leveling holes have broken off bolts in them. Both of which have no good purchase – one not at all and the other just a useless fragment of remaining bolt.
I have done my fair share of removing rusty screws from engine blocks using various methods but have never removed anything this substantial and or anything this seemingly “STUCK” before. These bolts are easily 5/8″ and the fact that they sheared off tells me they are really really stuck.
Option 1: Go the nuclear route and weld a nut onto them and see if I cant get them out. Penetrating oil does seem to absorb into these so maybe that is a good sign they might come free. I would really like to use these original leveling holes if I can.
Option 2: Go less nuclear and drill/ez-out method with much heat. As mentioned the fact that they sheared off in the first place leads me to believe this wont end well.
Option 3: Forget about them and just use the other holes with adjustable leveling feet. I like this less as I feel they put the leveling feet in the original spots for a reason and that they are the best place for them (maybe overthinking this).
Update 1: went with Option 2 to start sans the heat (did not have time to remove skid cross member). Well well, started drilling the one that was flush and if the damn thing didn’t start moving! I will take that win. Second one, well not so much fun yet. Drilled out 3/8″ hole and used 1/2″ ez out with not a budge. Heat comes tomorrow.
Ground off stump Started pilot 3 to 4 more drill sizes up to 3/8″ 1/2 EZ-OUT
One last soak in Penetrating Oil over night and again at lunch time – soak overnight did nothing, don’t expect latest soak to help much either. Torch time tonight.
Torch work did not cut it….could not get bolt hot enough. Went down the continue drilling route and re-tapped it. It worked better than expected and in short time have the hole finished an tapped.
3/4 16 Tap Success